INDUSTRIES SERVED NATIONWIDE
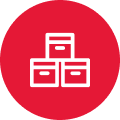
FOOD STORAGE
AND SHIPPING
FW Logistics provides certified food storage and shipping solutions, offering temperature-controlled and ambient warehousing to ensure the safety and quality of food products
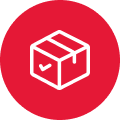
CONSUMER
PACKAGED GOODS
Collaborating with manufacturers and distributors to provide appropriate storage facilities. Offering cold storage and refrigerated trucking to maintain top quality.
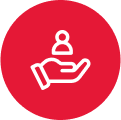
PERSONALIZED
CUSTOM SOLUTIONS
Fulfill your unique needs by taking advantage of our flexible storage and shipping options. Learn how our team can accommodate needs of any size.
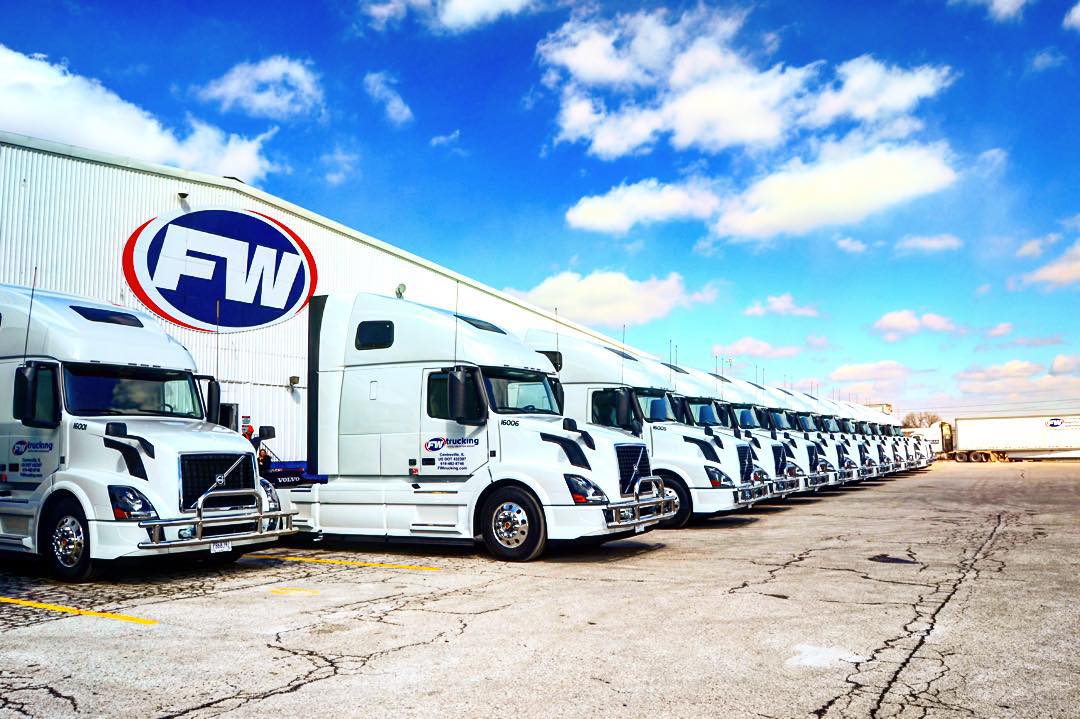
SINCE 1949
FW Logistics is an experienced logistic service provider that is big enough to handle all your supply chain logistics needs while still being small enough to give you specialized service.
Today, FW Logistics operates over 7 million square feet of warehouse facilities across the United States. The company prides itself on its core values of honesty, respect, and customer prioritization.
OUR WAREHOUSE FACILITIES ARE EQUIPPED TO MEET YOUR NEEDS
FW offers a comprehensive range of facility equipment designed to meet the diverse needs of their clients. Facilities are equipped with state-of-the-art technology to ensure efficient and safe handling of all goods.

TEMPERATURE CONTROLLED

BLAST FREEZING

FOOD-GRADE WAREHOUSING

FLEX SPACE

CHEMICAL & HAZMAT CERTIFIED

DRY STORAGE
IT’S PERSONAL
At FW Logistics, we understand not everyone runs the same way. Let us help you Identify:
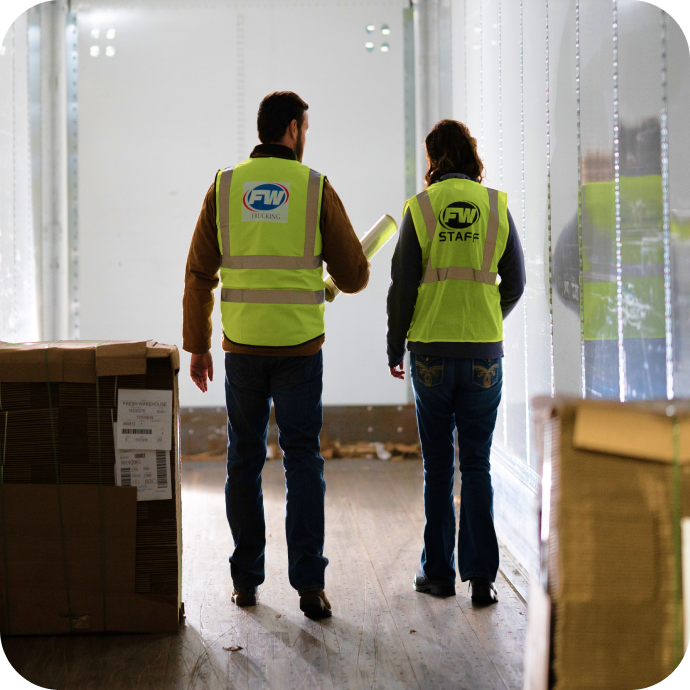
COMPANY CERTIFICATIONS & PARTICIPATION
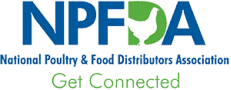



